Er zijn meerdere disciplines nodig om een schip te bouwen. In navolging van het Nader bekeken: de piping werkzaamheden voor het project Yacht Support Vessel-artikel van vorig jaar, geeft dit artikel een momentopname van Damen Naval’s ‘Manufacturing Engineering’ en ‘Cutting & Bending’ activiteiten die plaatsvinden in Vlissingen-Oost. Peter Ridderbos en Sandy Hubregtse hebben samen meer dan genoeg ervaring om inzicht te geven in dit cruciale aspect van het scheepsbouwproces. Peter werkt al 40 jaar voor Damen Naval, waarvan de eerste 16 jaar in de productie en sinds 1998 als Manufacturing Engineer, voornamelijk binnen de afdeling Structures. Sandy werkt al bijna 31 jaar voor Damen; zijn functie is Meewerkend Voorman voor de Werkvoorbereidingsactiviteiten. Hun respectieve rollen in Manufacturing Engineering en Werkvoorbereiding vormen de sleutelverbinding tussen Engineering en de eerste lassen die het begin van de fabricage markeren.
Peter begint met enkele definities: “Mijn werk richt zich op ‘structures’ – dit is de constructie van de romp, die altijd is verdeeld in een aantal secties of ‘blokken’. Elke sectie bestaat uit allerlei staalwerk, zoals panelen, dekken, schotten en knieën. Structures omvat al dit staalwerk en al dit staal wordt gesneden uit platen of profielen. Structures omvat ook de zogenaamde pre-outfitting, dat is het samenstellen en lassen van alle mogelijke fundaties die nodig zijn voor de scheepsuitrusting.” Over het algemeen maakt Peter deel uit van een team van twee personen, hoewel het team werd uitgebreid naar vier personen tijdens de recente Midlife Update van Zr.Ms. Johan de Witt.
“Elk schip of jacht waaraan we werken is bijzonder, maar de LCF-schepen voor de Koninklijke Marine springen eruit vanwege de dikte van de materialen die we gebruikten." Sandy Hubregtse
In zijn rol van Manufacturing Engineer krijgt Peter de input voor zijn werk van de engineering teams van Damen. “Dit komt bij ons binnen in een CADMATIC 3D-model per sectie van het schip”, legt hij uit. “Mijn taak is om deze informatie om te zetten in een logische bouwvolgorde van de sectie en van hieruit productie-informatie te genereren voor de voorbewerking voor het snijden van de stalen platen en profielen.” Behalve dat hij zorgt voor een continue stroom van het materiaal door Productiehal 1 in Vlissingen-Oost, gaat het bij Peters werk ook om het creëren van efficiëntie. “We snijden het staal uit platen van twaalf meter lang en drie meter breed. Het in-nesten van een ruwe plaat met de plaatonderdelen is een soort puzzel, maar we proberen ervoor te zorgen dat we zo min mogelijk afval hebben.” Belangrijk is dat niet al het werk van Peter gericht is op de productie in Vlissingen-Oost; de Manufacturing Engineering opdrachten die hij maakt, gingen in het verleden ook naar buitenlandse werven zoals voor de Indonesische en Mexicaanse marine projecten.
Terwijl Peter zijn werk digitaal ontvangt, is zijn output analoog. “Alles staat nog op papier”, zegt hij. “Al denk ik wel dat we in de komende vijf jaar een omslag zullen zien naar een meer 3D-output met tablets in de productiehal.”
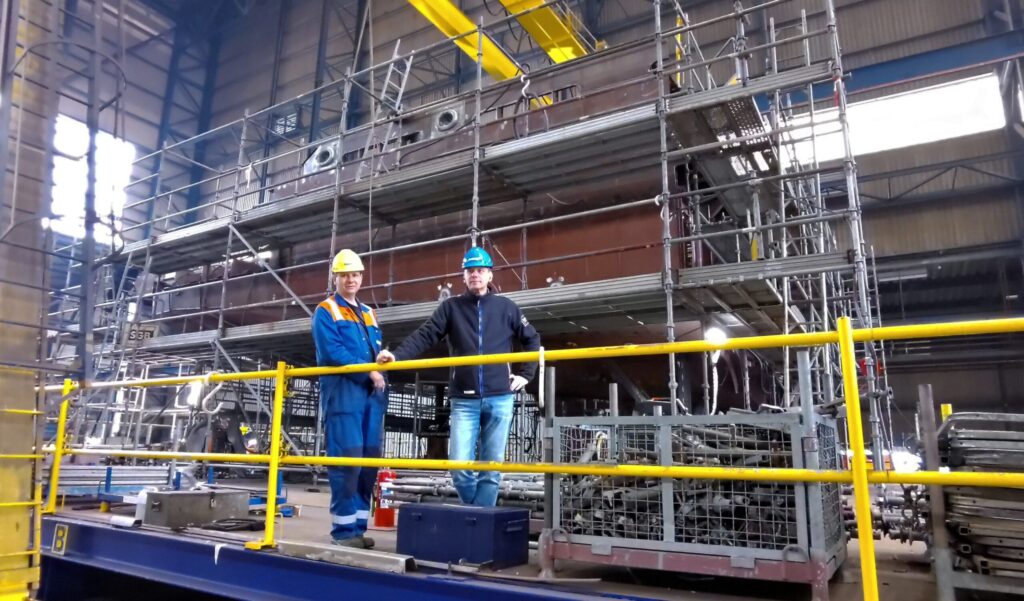
Sandy’s werk vormt de volgende stap in de workflow; hij voert de opdrachten uit die in de snijplannen voor staalplaat en profielen zijn vastgelegd. Als je bedenkt dat één sectie van een schip doorgaans uit zo’n 2.500 tot 3.000 stukken staal kan bestaan, en het huidige rompbouwproject YN 478 in totaal 14 secties telt, is het aantal afzonderlijke onderdelen dat door zijn handen gaat enorm. “Het is een klus die in de loop der jaren sterk is geautomatiseerd,” zegt hij. “Het gaat tegenwoordig zeker sneller. Vroeger werkten er tientallen mensen aan, maar nu werk ik met een team van zeven of acht mensen.”
De snelheid van de werkzaamheden in de productiehal is te danken aan twee hypermoderne plasmasnijmachines. “De Messer snijmachine behandelt de stalen platen en de HGG-profielrobot snijdt de profielen. Beide machines zijn snel, nauwkeurig en kunnen onder een hoek snijden voor de afgeschuinde randen”, legt Sandy uit. “We hebben ook een nieuwe roterende borstelmachine die we gebruiken voor het ontbramen en kantafronden na het snijden – zodat de oppervlakken en randen van het staal klaar zijn voor het lassen en verven.”
Ondanks de hightech apparatuur waarover Sandy en zijn collega’s beschikken, is er geen vervanging voor goede, ouderwetse ervaring en communicatie. “Wanneer je een sectie moet fabriceren, is de praktijkervaring zeer noodzakelijk. En we hebben regelmatig voortgangsvergaderingen omdat het, zeker in het begin van een project, erg druk is en we zo snel mogelijk veel onderdelen moeten leveren. Het is heel belangrijk om je aan de planning te houden.”
Gezien hun gezamenlijke ruim 70 jaar aan ervaring, rijst de vraag of Peter en Sandy een favoriet hebben onder een van de vele projecten waaraan ze hebben gewerkt. “Elk schip of jacht waaraan we werken is bijzonder,” antwoordt Sandy, “maar als ik één project in het bijzonder zou moeten kiezen, dan springen de LCF-schepen voor de Koninklijke Marine er in mijn herinnering uit vanwege de dikte van de materialen die we gebruikten.” Peter kijkt terug op de M-fregatten als zijn favoriet: “Dit was in mijn begindagen hier bij Damen, in de jaren tachtig; op deze schepen heb ik alle ervaring opgedaan die ik nodig heb voor mijn huidige werk.”