Slechts zeven jaar zat er tussen project kick-off en productie: een recent R&D-project heeft in een zeer kort tijdsbestek resultaten geboekt. “De snelheid van dit project was eigenlijk zeer indrukwekkend”, zegt Robbin Suiker, Engineer bij Damen Naval. “Bovendien heeft het project geleid tot echte innovatie.”
Robbin heeft het over een internationaal technologieproject onder leiding van TNO om de volgende generatie explosiebestendige schotten (blast bulkheads) te ontwikkelen. Damen Naval was een belangrijke deelnemer, samen met TKMS (Duitse scheepswerf) en SSAB (Zweedse staalleverancier). De Nederlandse Defensie Materieel Organisatie (DMO) en haar Duitse tegenhanger BAAINBw waren twee belangrijke belanghebbenden als mogelijke eindklanten.
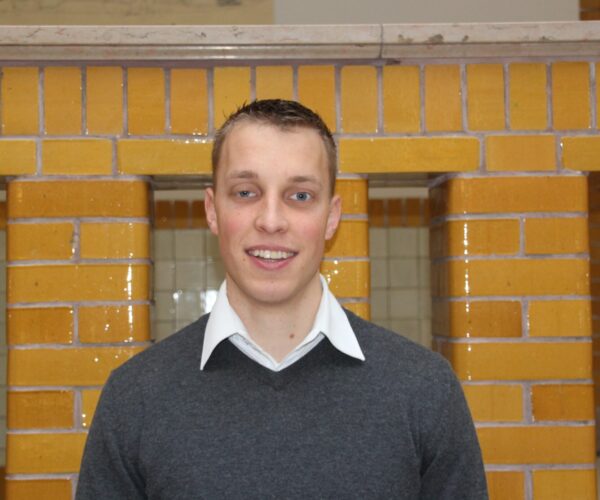
De typische functie van een “normaal” waterdicht schot is te voorkomen dat water van het ene naar het andere deel van het schip stroomt als de scheepsromp beschadigd raakt. Een zogenaamd blastschot is ook bestand tegen explosies. “Ondanks het ontwerpen van moeilijk detecteerbare schepen, goede radars en wapensystemen voor nabijverdediging op korte afstand, worden schepen toch geraakt door (anti-scheeps)raketten. Als een schip wordt geraakt door een anti-scheepsraket, beperken blast bulkheads de effecten van de inslag. Zij voorkomen dat de gevolgen van de ontploffing zich verspreiden over de rest van het schip en schade toebrengen aan personeel en materieel.”
Hoewel het concept van een blast bulkhead niet nieuw is (ze zijn geïnstalleerd op eerdere projecten), begonnen de deelnemers aan dit project vanaf nul “met een leeg vel papier, conceptueel denkend over hoe we alle vereisten konden integreren in een lichtgewicht en betaalbaar blast schot”.
Robbin beschrijft de bijdrage van Damen aan het project: “Als scheepsbouwers was het onze rol om een oogje in het zeil te houden bij de integratie van de nieuwe ontwerpen in een schip. We namen deel aan brainstormsessies, gaven advies over de praktische haalbaarheid, beoordeelden concepten en gaven advies over de kosten en de gevolgen voor de fabricage.” Daarnaast werd de productieafdeling van Vlissingen-Oost bij het project betrokken. “Dit was een perfecte gelegenheid om ervaring op te doen met het produceren van dit soort complexe schotten. Het was een uitdagend project met zeer strenge eisen en uitgebreide kwaliteitscontrole.”
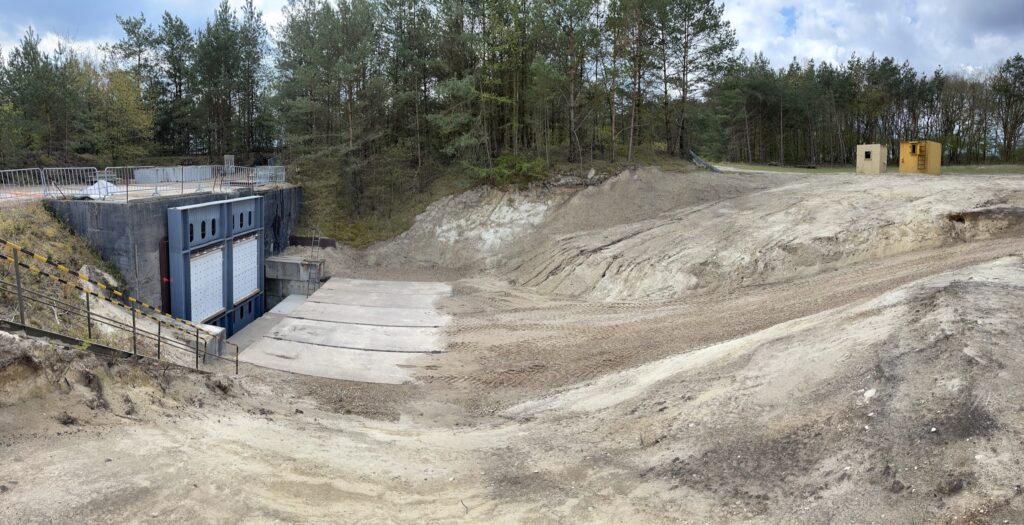
Na uitgebreide testen, uitgevoerd door TNO in de testfaciliteiten WTD 41 van het Duitse ministerie van Defensie, werd het project vorig jaar afgerond met de validatie van twee multifunctionele schotontwerpen. Robbin legt uit dat de nadruk ligt op het woord “multifunctioneel”. “Dit was de grote innovatie die het project heeft voortgebracht. Want het zijn niet alleen blast bulkheads met brandwerende en waterdichte eigenschappen, het zijn ook fragment-werende shotten die scherven tegenhouden én die brandwerend blijven na wapeninslag.”
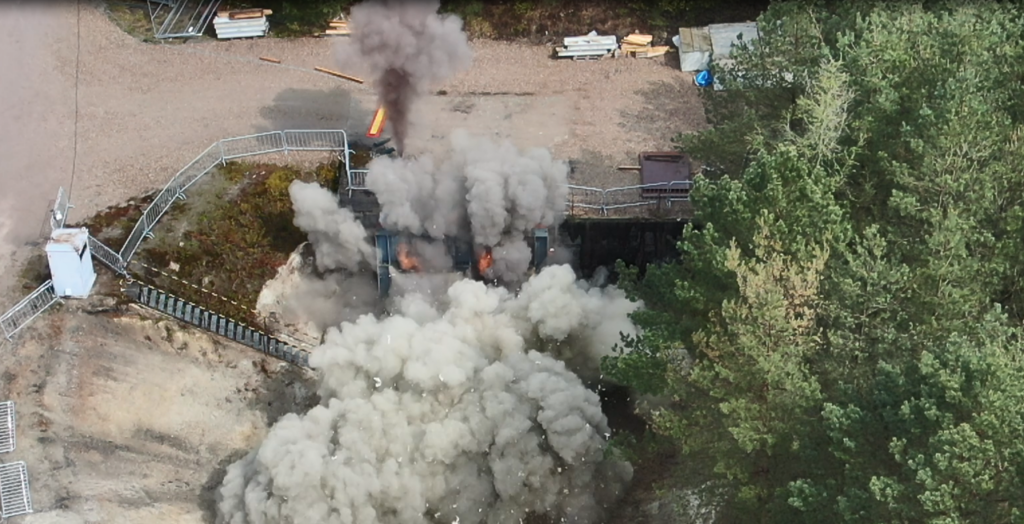
De capaciteit om scherven te stoppen is het meest relevant wanneer men een hypothetische raketinslag bekijkt. Niet alleen de ontploffing veroorzaakt schade; de raket explodeert in een groot aantal fragmenten. “Deze kleine stukjes metaal verplaatsen zich met duizenden kilometers per uur door het schip en hebben een grote reikwijdte, verder dan de ontploffingsstraal, en beschadigen alles wat ze passeren. Deze nieuwe schotten voorkomen dat.”
Het project heeft twee ontwerpen opgeleverd. De lichtere variant wordt geïnstalleerd in de nieuwe ASWF-schepen en de goedkopere variant zal zijn werk gaan doen aan boord van het Combat Support Ship dat momenteel in aanbouw is in Roemenië. “Het project heeft zich ontwikkeld van een leeg vel papier in 2015 tot een innovatief en gevalideerd ontwerp dat in een marineschip wordt geïntegreerd en aan de klant wordt geleverd, en dat alles in minder dan tien jaar tijd”, concludeert Robbin.