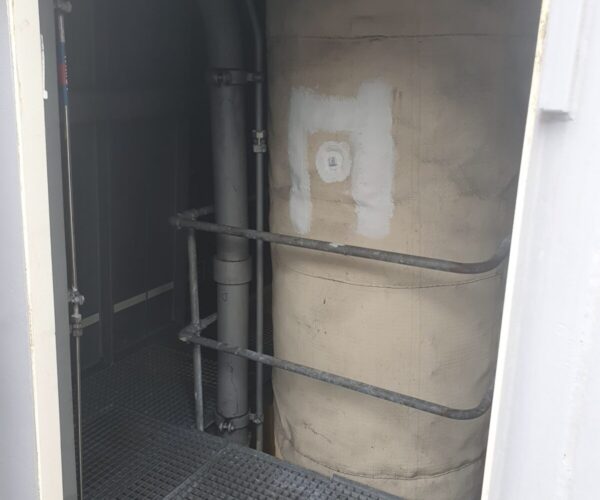
Last September, Damen Schelde Naval Shipbuilding carried out an extensive programme of onboard measurements to verify whether the measures for improving the HNLMS Karel Doorman’s ventilation systems had proved effective.
In 2014, exhaust gas particles were discovered in the fresh air ventilation systems on board the Joint Support Ship.
The problem, which posed a health risk to the crew of the largest ship of the Royal Netherlands Navy, was subsequently addressed by positioning the ventilation intake points further away from the exhaust pipes using plastic tubes. Furthermore, in 2019, the ventilation system was made adjustable.
This meant that, depending on the wind direction, fumes from the exhaust pipes would be directed away from the ventilation intake points.
Damen Schelde Naval Shipbuilding developed a special computer simulation to relocate these ventilation intake points. This calculated precisely how the plume of exhaust gases dispersed from the exhaust pipes at various wind angles and speeds.
Last September, a team from DSNS carried out extensive ‘exhaust gas validation measurements’ on board the Joint Support Ship to determine whether the measures taken as a result of the computer simulation had worked. DSNS took exterior measurements at the same time that the Royal Netherlands Navy took measurements from inside the ship.
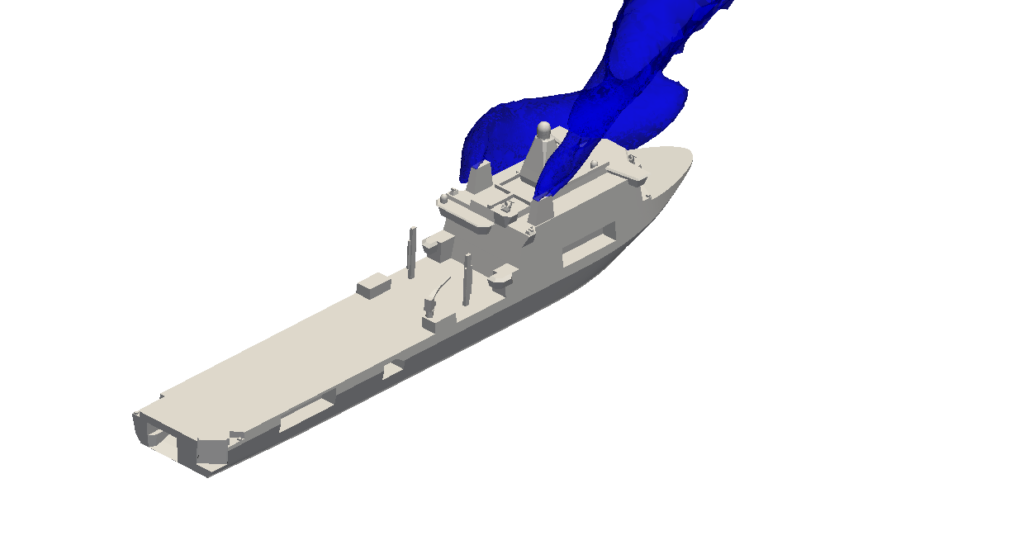
“With the help of sensors in all kinds of places on the HNLMS Karel Doorman, we measured the concentrations of exhaust gases at various wind speeds and various directions, and with different diesel configurations, ” says Project Director Arjan Risseeuw.
“For the purpose of the study, we even placed ‘sniffers’ in the diesel exhaust pipes. With the results of the measurements, we were ultimately able to determine whether the ‘exhaust gas plume’ that the computer simulation had calculated corresponded with the exhaust gas concentrations we actually measured throughout on the ship.”
In other words, the research showed whether the approach to the exhaust gas problem in the ventilation systems had been sufficient and whether the simulation model predicted the plume correctly.
Looking back on the research, Arjan notes: “Regarding the exhaust gases in the ship, some further refinements are needed to look at the right time to deploy the wind measurement installation; DMO has started an investigation for this. With regard to the validation of the model, results can be expected by the end of this year.”
The results of these validation measurements will then be processed into a computer model, which can be used in the construction of ventilation systems of future DSNS ships, says the Project Director. These include the successors of the Multipurpose frigates.