Working for Damen Naval doesn’t necessarily mean being based in Vlissingen or even the Netherlands; there are currently quite a few Damen Naval people working abroad. Two key areas in which these people work are Production and Services; these departments are managed by Martin Wattel and Frank den Hollander respectively. This article is the first in a series that will find out more about who is currently working abroad, what their role is, and what motivated them to take on this task. But first, it’s time to speak to Martin and Frank to gain a broad overview of Damen Naval’s Production and Services activities taking place around the world.
In terms of Production, there are numerous reasons that Damen Naval posts its own teams at foreign shipyards. “Of course, keeping an eye on quality is important,” says Martin. “But we also help these partner yards with the complexity of projects. We have processes to build naval vessels, and we have developed these to make it possible for other countries to work with that.”
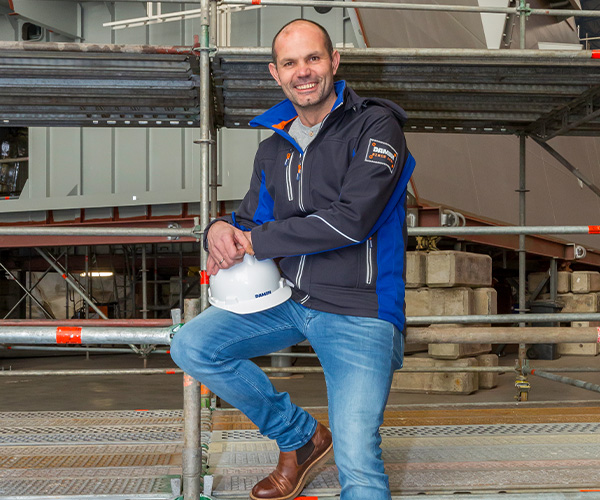
As Head of Production, Martin is currently coordinating teams in various countries. “We have assembled the site teams for Wolgast and Kiel in Germany for the F126 project. And we have people in Galați too, working on the CSS. We lend people to other Damen entities when they need specific knowledge as well; so right now, we have a supervisor working on a project for Damen Shipyards Cape Town. Broadly speaking, these teams provide on-site support and guidance at the yards, supervising the local teams in our way of working.”
The supervision of production at foreign yards can be divided into different levels. Taking the F126 project as an example “we have a subcontract manager, two site managers in Wolgast and Kiel” adds Martin. “And then we have the supervisors working under them – these are for the various disciplines such as welding, steel hull building, piping, mechanical, as well as manufacturing engineering, which involves getting the production information ready and aligned with the yard.”
As the Production process comes to an end, the subject of Services comes into play. Frank den Hollander defines the Service department’s role as “being responsible for the commissioning of the vessel, the sea trials, the warranty period, and the service support for the lifetime of the ship”. Looking at the international nature of Damen Naval’s clients, it’s not surprising to learn that a lot of this work takes place abroad. The commissioning of the Mexican POLA frigate and the Nigerian Navy LST 100, for example, both took place in the country of construction. The Mexican POLA frigate was built locally in Mexico and the LST 100 was built at Damen Shipyards Sharjah in the United Arab Emirates. Depending on the needs of the project, commissioning teams generally work on a rotation basis of six weeks on followed by two weeks at home or similar.
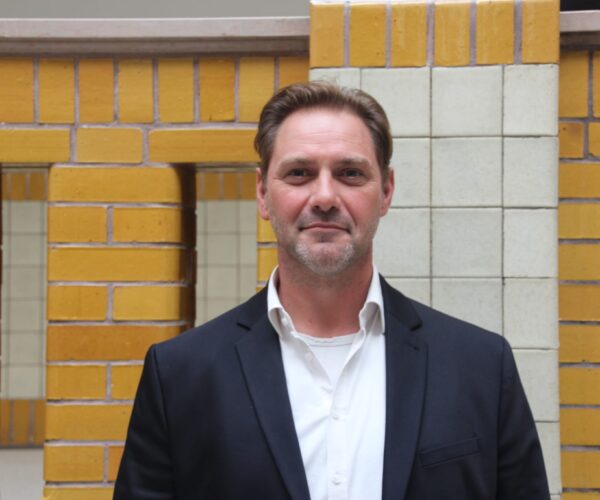
During the warranty period, Franks says that it “is important that we have direct contact with the people who are actually sailing on these ships as well as their onshore support teams”. This is why Damen Naval’s Warranty Engineers are based at (or close to) the vessel’s home port. “We are currently rounding off the warranty for the Nigerian Landing Ship, for this we have been working together with the Damen service Hub in Nigeria. And for the icebreaker Nuyina – we have a dedicated engineer living in Tasmania.” Read more about the work of the Nuyina’s Warranty Engineer Michiel Schittekat in this previous Schelde Schakels article.
In addition to serving as a client’s first point of contact, deploying a Warranty Engineer is also about gaining valuable information about the ship in question. “We ask a lot from the people that we have working abroad, they have a lot of responsibility. Part of this is to stay connected with the client and the ship; this is an important part of how we work; it’s how we find out how our ships operate and if we can improve our designs,” he adds. This connection to the client can continue after the warranty period when the client prolongs its relationship with Damen in the form of a service contract. “Our work in Morocco is a current example of a service contract, where we have an engineer on site who is the first point of contact for the client.”
The length of time that people spend abroad varies; some people decide to move abroad for the duration of the entire project, others opt to shuttle back and forth on a ‘three weeks abroad/one week in the Netherlands’ basis. “It depends on their personal situation; we don’t force anyone to work abroad. But some people love it, bringing their experience and knowledge to another country,” Martin says.
Whether they are based in Tasmania, Indonesia, Nigeria, Germany or any other country, Damen Naval’s ‘ex-pat’ workers surely have interesting stories to tell. We will be discovering more of these in future issues of the Schelde Schakels.