Seven years from project kick-off to production: a recent R&D project has achieved results in a very short timeframe. “The speed of this project was actually very impressive,” says Robbin Suiker, Engineer at Damen Naval. “Moreover, the project has led to true innovation.”
Robbin is talking about an international technology project headed by TNO to develop the next generation blast-resistant bulkheads. Damen Naval was a key participant, together with TKMS (German shipyard) and SSAB (Swedish steel supplier). The Dutch Defence Materiel Organisation (DMO) and its German equivalent BAAINBw were two important stakeholders given their ability to act as potential launching customers.
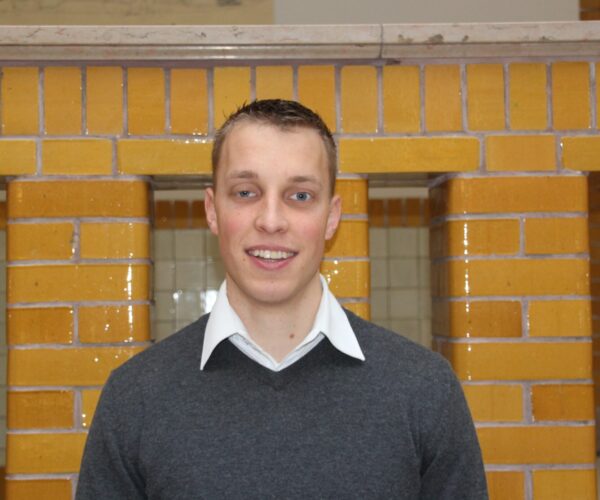
The typical function of a ‘normal’ watertight bulkhead is to prevent water flowing from one area of the ship to another in the event of a hull rupture. A so-called blast bulkhead is also blast-resistant. “Despite low signature designs, good radars and close-in weapon systems, ships have been hit by (anti-ship) missiles. If a vessel is hit with an anti-ship missile, blast bulkheads confine the weapon effects. They prevent the effects of the blast spreading throughout the rest of the ship and damaging personnel and materiel.”
While the concept of a blast bulkhead is not new (they have been installed on previous projects), the participants in this project started from scratch “with a blank piece of paper, thinking conceptually about how we could integrate all requirements into a lightweight and affordable blast bulkhead”.
Robbin describes Damen’s contribution to the project: “As shipbuilders, our role was to keep an eye on the integration of the new designs into a ship. We participated in brainstorm sessions, gave advice on practical feasibility, judged concepts and gave advice on cost and manufacturing implications.” In addition, the project involved the production department at Vlissingen-Oost. “This was a perfect opportunity to gain experience with producing this type of complex bulkhead. It was a challenging project with very tight tolerances and extensive quality control.”
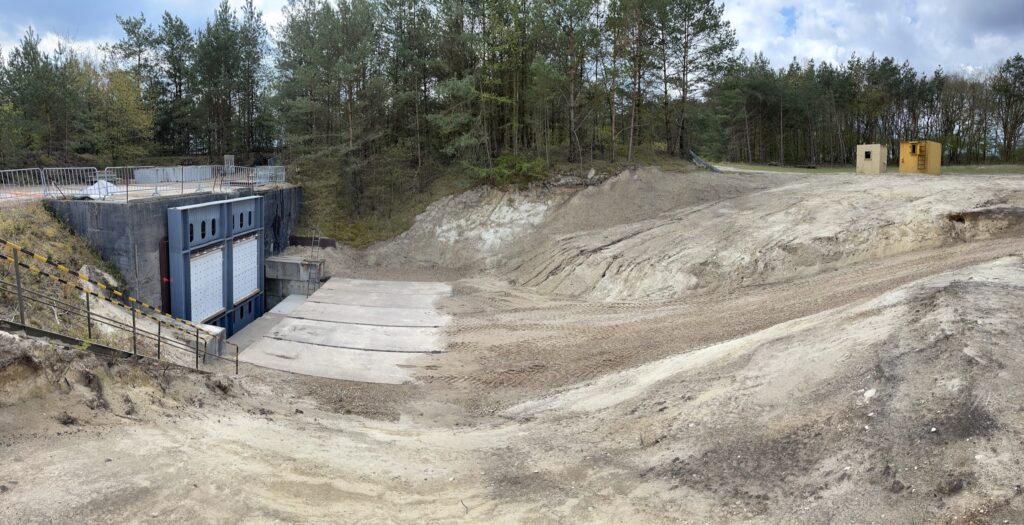
After full-scale testing carried out by TNO at the German Ministry of Defence testing facilities WTD 41, the project was finalised last year with the validation of two multifunctional bulkhead designs. Robbin goes on to say that the word ‘multifunctional’ is key here. “This was the big innovation generated by the project. Because they are not only blast bulkheads with fire resistant and watertight characteristics, they are also fragment retaining bulkheads and remain fire resistant after weapon impact.”
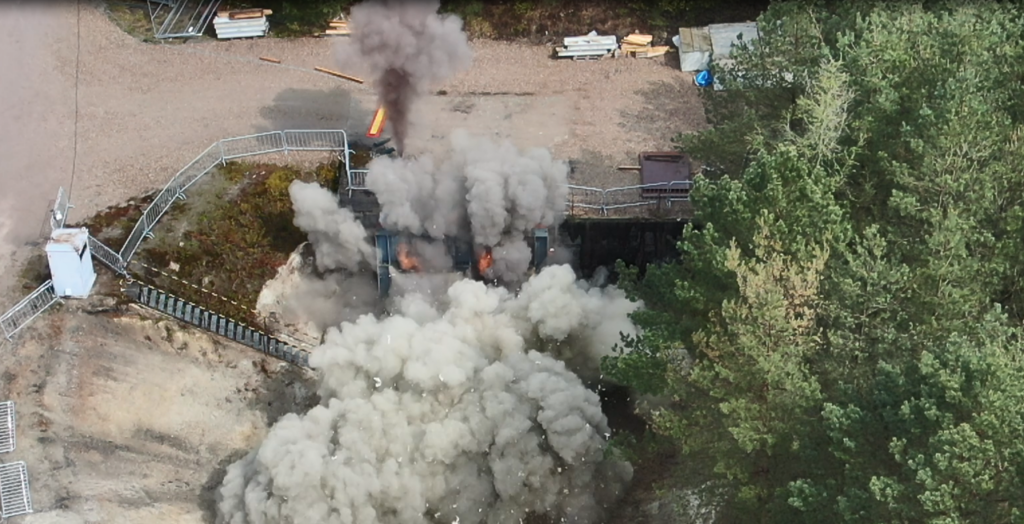
The fragment retainment capacity is most relevant when looking at a hypothetical missile strike. It is not only the blast that causes damage; the warhead explodes into lots of fragments. “These tiny pieces of metal travel at thousands of kilometres an hour a long way through the ship, further than the blast radius, damaging everything they pass. These new bulkheads prevent that from happening.”
The project yielded two designs. The lighter variant will be installed in the new ASWF vessels and the cheaper one will deliver its prowess to the Combat Support Ship that is currently under construction in Romania. “The project went from a blank piece of paper in 2015 to an innovative and validated design that is integrated in a naval vessel and delivered to the customer, all in less than ten years,” concludes Robbin.