It is a marvellous acquisition and the Work Preparation team of the Production Department are very proud of the brand-new Messer cutting machine that Damen Naval has purchased. The impressive installation can cut steel plates with great precision, from very small pieces up to 12×3 metres in size. In addition, the machine can apply dimension lines and text to plates to be cut. The machine’s cutting table is self-cleaning, which is another big advantage. Its predecessor always had to be taken out of service for a few days when it needed to be cleaned.
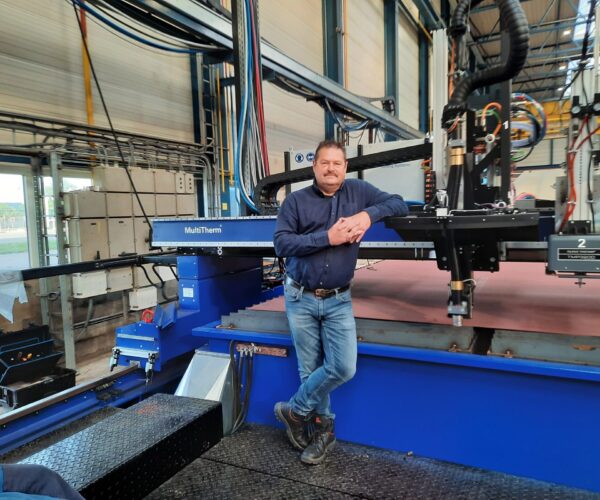
It was high time to replace it: the steel cutting machine that Damen Naval had used at Vlissingen-East’s Work Preparation until this year. That “solid old beast”, as Production Coordinator Ronald de Baar affectionately calls the machine, was already in use in the former Heavy Steel Plate Workshop in the old Vlissingen city site. “When I started at Damen in 2005, they were just in the process of moving it to East, where Work Preparation was under construction at the time,” Ronald explains. But now, after 30 faithful years of service, the cutting machine has been taken out of service and disposed of, and in the large hall of the Work Preparation Department there is a brand new cutting machine that, like its predecessor, was made by Messer Cutting Systems.
“The new cutting machine is a huge boost for our department. This investment is important for our entire construction process." Ronald de Baar
“We are very happy with it,” says Ronald. “It gives us at Production a good feeling that this investment has been made.” In August, the cutting machine chassis was already installed in Vlissingen-East: the rails and the two cutting tables. On Friday morning, 3 September, the superstructure arrived: the gantry with all the components needed to perform the cutting and marking work. The gantry can move from one cutting table to another on the rails and the cutting components can be moved in different directions. “The great advantage of this cutting line is that it can cut bevelled – i.e. diagonal – edges,” says Ronald enthusiastically.
“This was not possible with the previous machine, which could only cut at right angles. When a part was cut, the welding edges had to be repositioned afterwards. The table of the new installation is also self-cleaning. A conveyor belt at the bottom continuously transports burnt residues from the cutting process – slag – and small parts to the starting point of the machine, where a grid separates parts and waste. The old cutting machine lacked such a conveyor belt. When the waste had to be removed, the installation was shut down for a few days. An external company then had to come and empty the waste bins.”
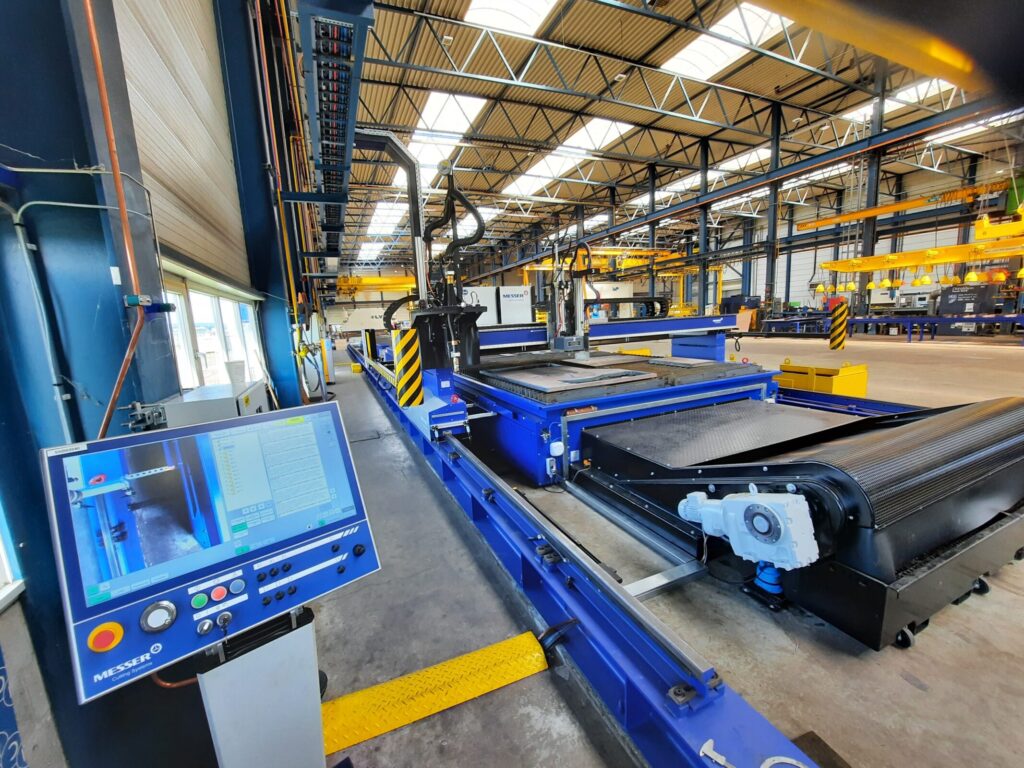
The air extraction system of the old Messer also suffered from vacuum loss when extracting the smoke. The new machine does not have this problem; it extracts the smoke downwards into the table. Controlled valves regulate the vacuum of the suction to the place where the portal actually cuts. Once extracted through pipes, the smoke is cleaned of dust in a filter unit located outside the building. The new system cuts with dry plasma and can also carry out marking as well as cutting. The plasma head can be used at low power to apply dimension lines to the sheets.
A matrix printer can engrave easily readable texts in the steel. This is necessary to be able to identify the cut sheets further along the shipbuilding process. The fact that the new machine has two cutting tables ensures that the cutting work can take place without interruption, which makes things progress smoothly, Ronald explains. When a plate has been cut on one table, the gantry moves over the rails to the second cutting table, where the next plate is already waiting. The first plate is then unloaded from the table in parts and sorted for the building process and any further finishing.

“We will use the plasma torch for about 95 percent of the regular cutting work needed,” says Ronald. “We can quickly and very accurately cut bevelled steel sheets up to a thickness of 50 mm. The maximum thickness for 90-degree plasma cutting is 80 mm. For thicker plates, we switch to the autogenous cutting process, which works with flammable gases, just like a cutting torch. That way we can only cut perpendicularly. For the switch from plasma to oxy-fuel, an optimum still needs to be found in practice. Ronald is “as proud as a monkey with seven tails” that the Messer has been purchased.
“It is a huge boost for our department,” emphasises the Production Coordinator. “This investment is important for our entire construction process. The quality of the cuts will be higher, which means that section fabrication can work more neatly and efficiently. The new machine enables us to keep the entire process in-house and not be dependent on external parties for cutting work. This allows Production to respond quickly to changing situations.” The purchase fits in with Damen Naval’s philosophy that to remain competitive as a shipbuilder you must continue to invest in equipment that is up to date.
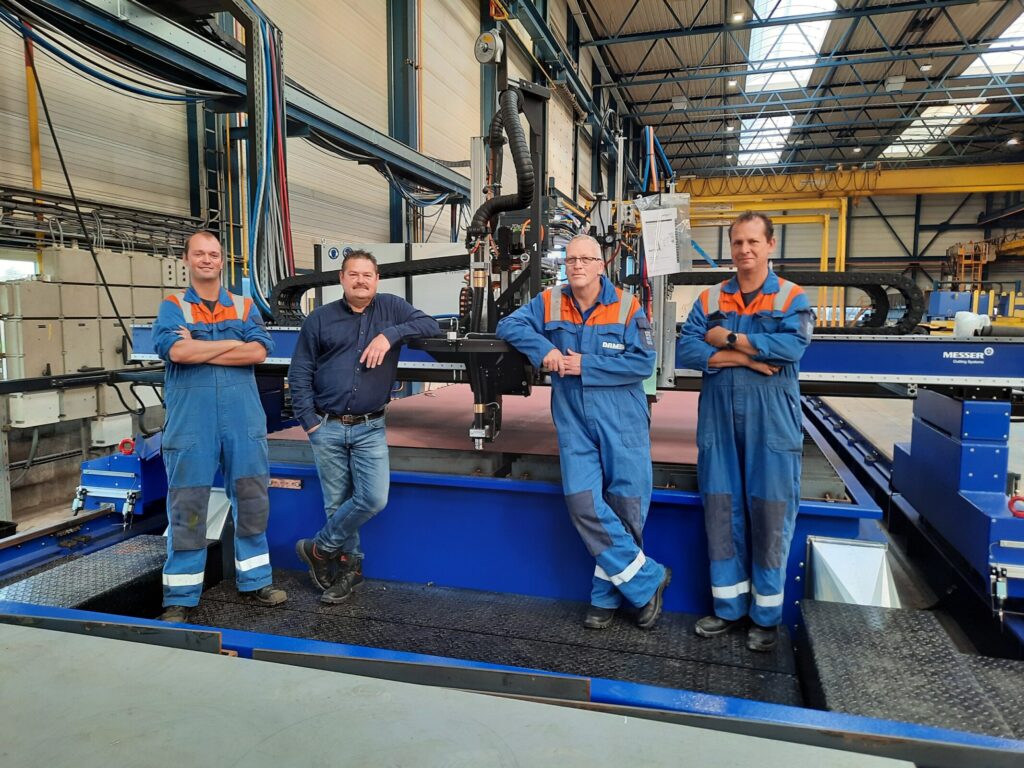
“With state-of-the-art equipment at our production facilities, we can continue to provide our customers in the various defence markets with superbly designed and built vessels,” says Director of Operations Tijs Buijs. The first major job for which the Messer will be used is the construction of a hull for a Yacht Support Vessel for Damen Yachting. “The customer wanted the hull to be built in the Netherlands,” says Production Coordinator Stan Haag, “while Damen Naval had just decided to revive Production; a nice coincidence.”
“We are busy recruiting new staff, from welders, metal workers and pipefitters to mechanical specialists, foremen and assistant foremen. Our employees are relatively old and when a large group of very experienced and skilled colleagues from Production retires, we hope that with this new influx we will be able to prevent a lot of knowledge and experience from being lost. But if you want to train these newcomers for Production, you need work for them. That is now available in the form of this project for Damen Yachting.”
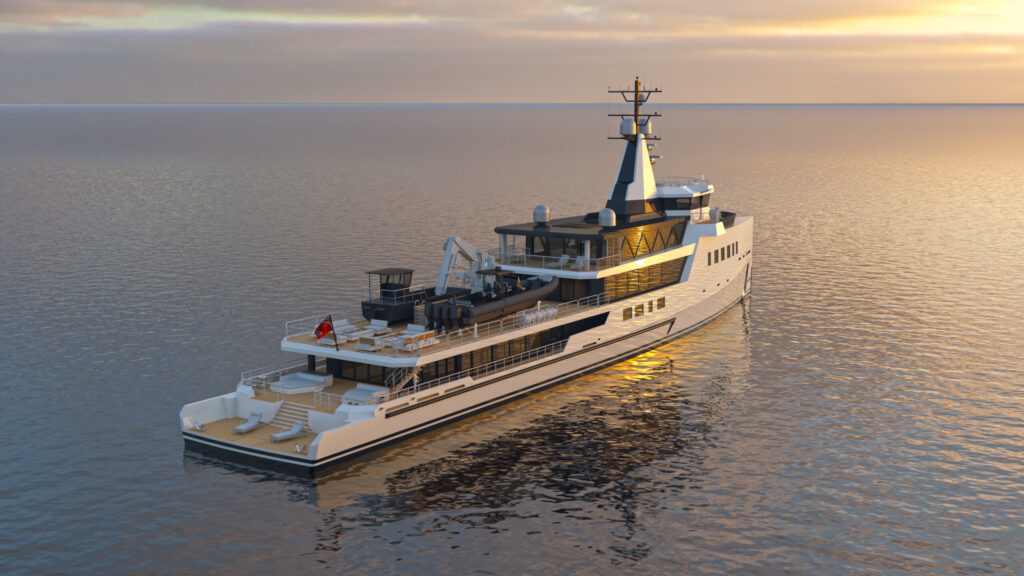
Damen Naval is also busy renovating its production facilities at the Vlissingen-East site. The purchase of the Messer cutting machine fits entirely in that picture, notes Stan. The hull for the 72-metre long and eleven-metre wide Yacht Support Vessel (construction no. 478 for Damen Yachting) will be completed in November next year. What is special about this project is that the vessel is actually a support vessel for a superyacht, and therefore one of the largest of its kind built by Damen. “We are doing a bit more than just the hull construction on this project, that’s the agreement,” says Stan.
“In addition to the steel construction, we are also responsible for the piping and a large part of the mechanical work, for example for the engines, air conditioning units and switchboards. We will put everything that is big and heavy in place and connect it to the piping where necessary.” The hull construction will take place in Hall 2 in Vlissingen-East. The hull will be assembled from a number of sections that will be made in advance on huge construction platforms, which Production is currently refurbishing for this project. The project underlines the excellent relationship between Damen Naval and Damen Yachting (and Damen Shiprepair as well), says Stan. He is very happy.
“There had been no classical shipbuilding work such as cutting, ironwork, welding and pipefitting performed in Vlissingen-East for a few years now. Thanks to this job, we will be busy again and that makes me happy and proud. We will hand over the hull officially to Damen Yachting in November 2022, who will then take care of the further outfitting. I invite everyone at Damen Naval to take a look at our production halls. You are welcome for a guided tour…!”
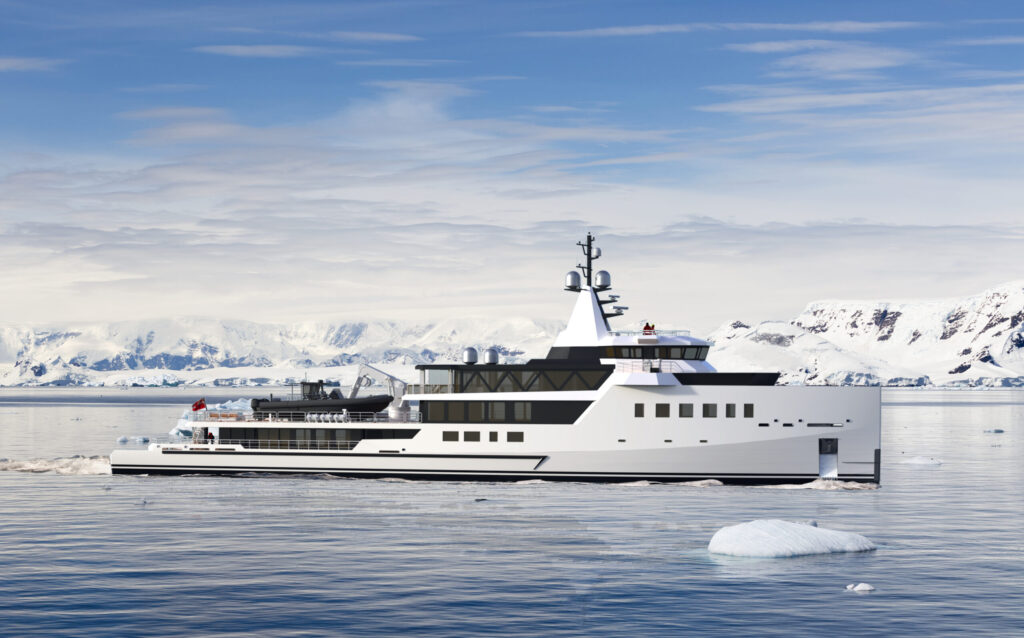