The steel construction department in Vlissingen-Oost is very happy with the new finishing machine that entered service just before Christmas. The Timesavers International machine deburrs and sands cut steel beautifully, while also ensuring perfect rounding of edges. Previously, this was all done by hand, but it was time-consuming, not as safe and produced a lower quality end result. Thanks to the new machine, steel finishing will now be more sustainable, says Production Coordinator Ronald de Baar. Coatings and paint adhere much better to the rounded corners.
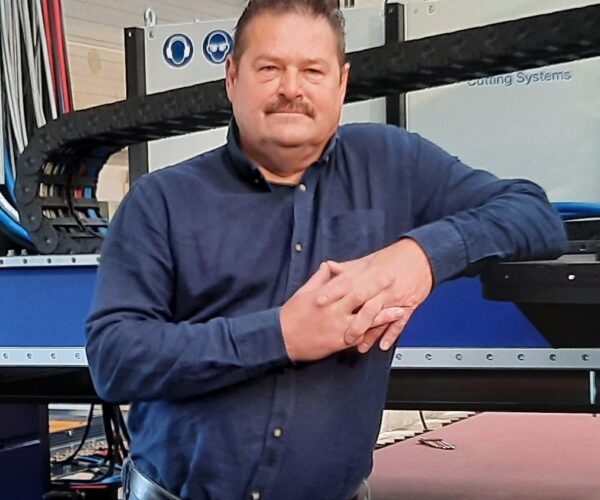
Damen Naval stumbled upon the new machine by accident, Ronald explains. “When we were looking for the new cutting machine, which we started using last year, we happened to see this finishing machine at a potential supplier. I didn’t even know machines like this existed! It turned out that it was also made in Zeeland, by the company Timesavers International in Goes, which has been in existence for seventy years.” Together with Yard Facilities Manager Frans Voermans, Ronald made a proposal to the management to request a quote from the Goes company.
After some calculations, it soon became clear that the purchase of the machine would save the equivalent of one fulltime job and result in a considerable quality improvement in steel processing. “The machine will probably pay for itself in about one year,” Ronald says. In the pre-processing area adjacent to Assembly Hall 1, Ronald shows us around and proudly demonstrates the new machine.
“The machine will probably pay for itself in about one year.” Ronald de Baar
The remarkably compact machine is equipped with a rotating brush unit with eight sanding brushes. This is used to treat the steel. Of the eight brushes, four rotate counterclockwise and four clockwise so that all corners and holes are worked and rounded. “The finishing machine is designed to process small to very small pieces of steel,” Ronald explains. “This would include parts such as knuckles, flanges and collar plates. The steel pieces are fed in via a conveyor belt and the same conveyor belt is used to take them out again when they are finished.”
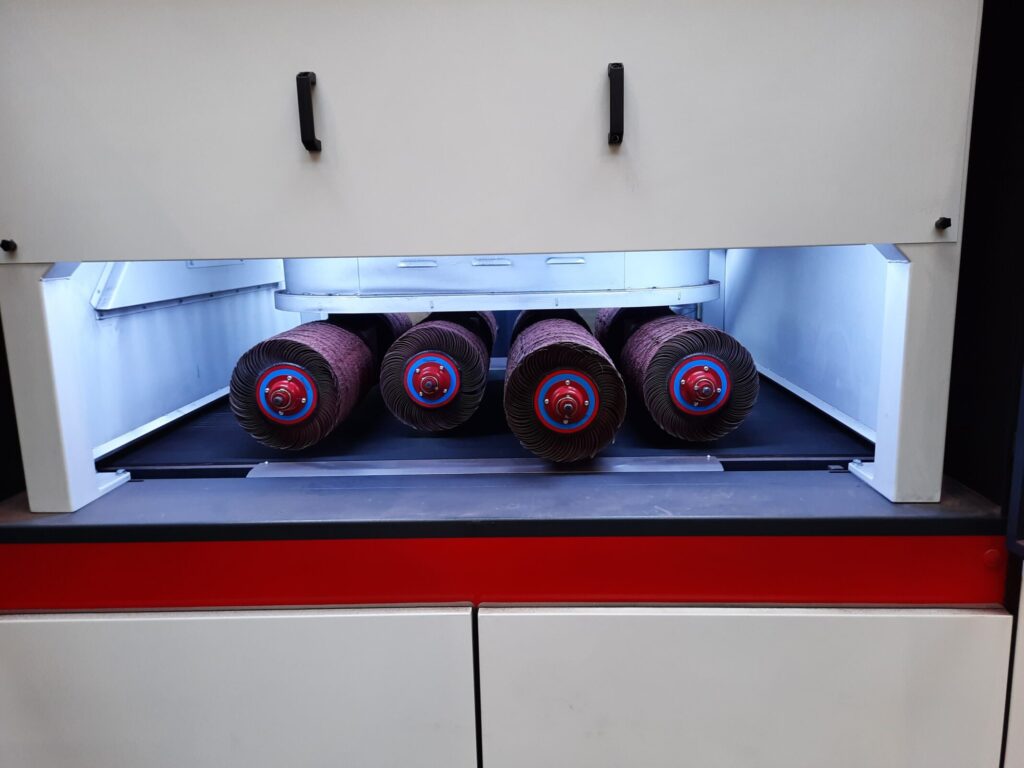
The conveyor appears to be equipped with a magnetic track to keep the steel parts in place. “The belt also has a clever vacuum system to hold non-magnetic material such as stainless steel and aluminium.” Thanks to the purchase of the new machine, type Grindingmaster 42-series-1350-Rb, steel finishing is now much faster than when they used to do it with a grinder at the pre-processing stage. This is because Timesavers International’s machine can process several steel pieces at the same time, Ronald explains. “And because a set of sanding brushes lasts at least a year, we also save a lot on abrasives.”
The new machine is an extension of the steel cutting machine. Because the cutting machine can run almost fully automatically, operator Dennis de Jonge can feed the new machine while he keeps an eye on the automated cutting process. The new acquisition is expected to last at least fifteen years, Ronald says. “And it might be nice to mention that the extractor we have fitted onto the machine is an old one that used to belong to the previous cutting machine. In this way, we are also doing our bit to stop the ‘disposable’ society.”