There are multiple disciplines required to build a ship. Following on from the ‘closer look at the piping team’ article last year, this article aims to give a snapshot of Damen Naval’s ‘Manufacturing Engineering’ and ‘Cutting & Bending’ activities taking place at Vlissingen-Oost. Peter Ridderbos and Sandy Hubregtse certainly have enough experience between them to give an insight into this crucial aspect of the shipbuilding process. Peter has worked for Damen Naval for 40 years, the first 16 of which were in Production, and since 1998 as a Manufacturing Engineer, primarily within the Structures department. Sandy has worked for Damen for almost 31 years; his function is Foreman for the Work Preparation activities. Their respective roles in Manufacturing Engineering and Work Preparation are the key link between Engineering and the first welds that mark the beginning of fabrication.
Peter begins with some definitions: “My work focuses on ‘structures’ – this is the construction of the hull, which is always divided into a number of sections or ‘blocks’. Each section is made up of a wide range of steel work: panels, decks, bulkheads, girders, for example. Structures includes all this steel work, and all of this steel is cut from either plates or profiles. Structures also includes the so-called pre-outfitting, which is the welding of all the possible foundations required for the ship’s equipment.” In general, Peter is part of a two-man team, although during the recent Johan de Witt MLU project the team was expanded to four people.
"Every ship or yacht we work on is special, but the LCF ships for the Royal Navy stand out because of the thickness of the materials we used." Sandy Hubregtse
In his role of Manufacturing Engineer, Peter receives the input for his work from Damen’s engineering teams. “This comes to us in a CADMATIC 3D model per section of the ship,” he explains. “My job is to convert this information into a logical order for the work preparation team to do their work of cutting the steel plates and profiles.” In addition to enabling a productive flow of materials through Production Hall 1 at Vlissingen-Oost, Peter’s work is also about creating efficiency. “We cut the steel from plates twelve metres long, three metres wide. It’s kind of a puzzle, but we try to make sure that we have as little waste as possible.” It is important to note that not all of Peter’s work is directed to production at Vlissingen-Oost; the Manufacturing Engineering assignments he produces are also sent to foreign yards such as for the Indonesian and Mexican naval projects.
While Peter receives his work input digitally, his output is analogue. “Everything is still on paper,” he says. “Although I do think we will see a change towards a more 3D output with tablets in the production hall within the next five years.”
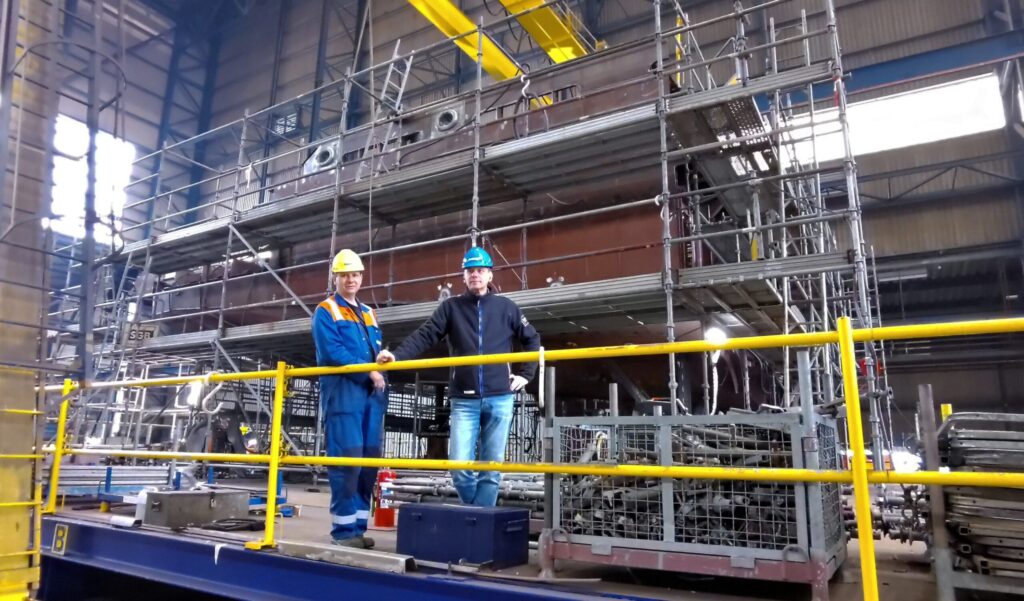
Sandy’s work represents the next step in the workflow; he executes the assignments stipulated in the steel plate and profile cutting plans. Taking into account that one section of a ship can typically consist of around 2,500 to 3,000 pieces of steel, and the current YN 478 hull construction project has a total of 14 sections, the number of individual parts that passes through his hands is huge. “It is a job that has become highly automated over the years,” he says. “It is definitely faster these days. There used to be dozens of people working on this, but now I work with a team of seven or eight people.”
The speed of operations in the production hall is due to two state-of-the-art plasma cutting machines. “The Messer cutting machine handles the steel plates and the HGG profile robot cuts the profiles. Both machines are fast, accurate and capable of cutting at angles for the bevelled edges,” explains Sandy. “We also have a new rotary brush machine which we use for deburring and rounding of edges after cutting – ensuring that the surfaces and edges of the steel are ready for welding and painting.”
Despite the high-tech equipment available to Sandy and his colleagues, there is no substitute for good ‘old-school’ experience and communication. “When you need to fabricate a section, the practical experience is very necessary. And we have regular progress meetings because, especially at the beginning of a project, it is very busy and we have to deliver a lot of parts as fast as possible. It’s very important to keep to the planning.”
With their 70+ years of experience, do Peter and Sandy describe one of the many projects they have worked on as a favourite? “Every ship or yacht that we work on is special,” replies Sandy, “but if I had to choose one project in particular, then the LCF ships for the Royal Netherlands Navy stand out in my memory for the thickness of the materials we used.” Peter looks back at the M-frigates as his favourite: “This was in my early days here at Damen, back in the 1980s; it was on these vessels that I gained all the experience that I need to do my current job.”