In the process of building a ship, the discipline of pipe installation is indispensable. Piping networks form a highly organised part of a ship’s functionality. Systems such as cooling, fuel storage and supply, drinking water and waste water all depend on a well-designed and expertly-installed piping system. Despite this vital role in a ship’s day-to-day operations, not much is known about the work of the piping teams in Damen Naval’s fabrication halls. Marco Gabriëlse and Jimmy Post who are both currently working on the YN 478 Yacht Support Vessel hull construction at Vlissingen-Oost, explain the ins and outs of their specialist jobs.
Marco (32) works as a Manufacturing Engineer; he joined Damen in 2006 and, after completing the in-house training programme, gained a permanent contract as a pipe fitter in 2007. Since then, he has worked on numerous projects including frigates for the Moroccan and Indonesian navies, Dutch patrol vessels, and the Joint Support Ship HNLMS Karel Doorman. Flexibility has been an important characteristic in his career path as he has worked on new build projects as well as refits and repairs, in addition to sometimes being ‘loaned out’ to Damen sister companies.
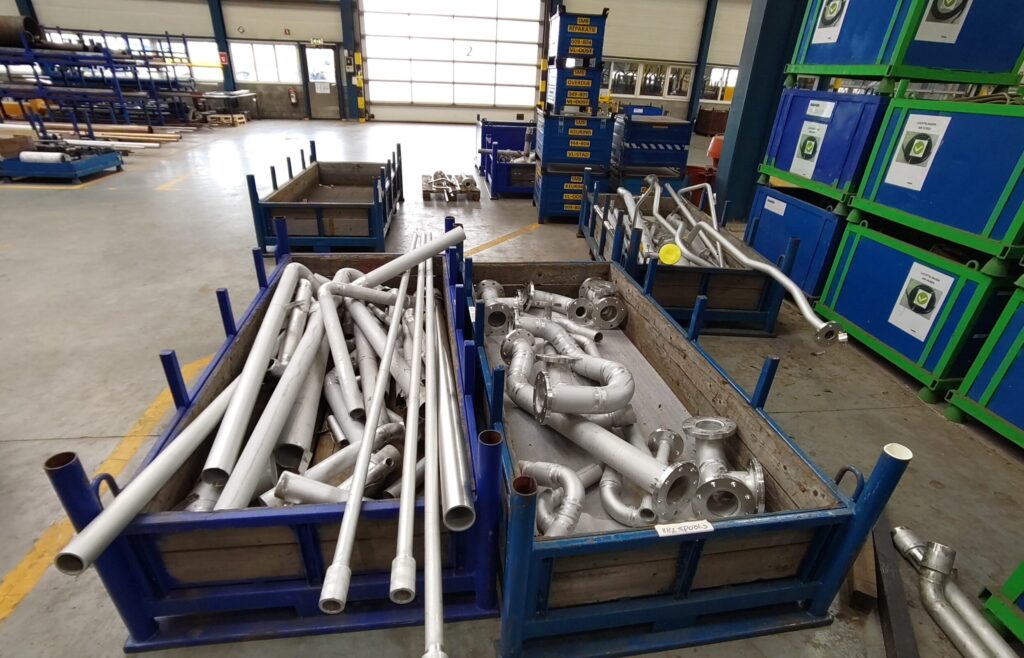
“Piping is divided into three separate phases,” Marco explains. “The first two phases are pre-outfitting and outfitting; these both involve installation of pipe spools [separate sections of pipe] that the team has pre-fabricated in the pipe shop. The third category is tubing. Pre-outfitting is the installation of piping in the walls and deck of the ship. This takes place during the construction of the sections. Taking the YN478 that we are working on now as an example, all this happens in production hall number one. The outfitting piping is all the pipework that has to be bolted down. For the YN478, this is generally what happens in hall number two. The third category is tubing. This is all the small pipe work, less than 30mm in diameter. This can be to connect previously installed piping – small pipes to pressure gauges, for example – or new pipelines such as hydraulic systems. This tubing is carried out in situ by a pipe fitter towards the end of construction.”
"In tubing, a pipefitter can decide for himself what the best route for a pipe is. Experience plays a major role, and it is here that you can see some real craftmanship.” Marco Gabriëlse
For the last four years, Marco has been responsible for the work preparation for the piping teams. Work preparation can best be described as the in-between step between engineering and actual production. “There are two of us working on work preparation for piping,” says Marco. “Our job is to get everything ready for fabrication in the pipe shop; from the raw materials to estimating how many people are needed for the workload and making sure that everyone knows exactly what to do. After the pipe spools have been made and, if necessary, painted and treated, we then organise assembly on board.”
As with many production specialities, there is a sense of craftmanship in piping. This is most noticeable, says Marco, during the tubing process. “Pre-outfitting and outfitting work are very much predetermined; the pipe fitters follow exact guidelines. Tubing, on the other hand, involves a pipe fitter walking on board with the purpose of fitting a pipe or tube from point A to point B. They can decide themselves which is the best route; therefore, experience plays a major role, and it is here that you can see some real craftmanship.”
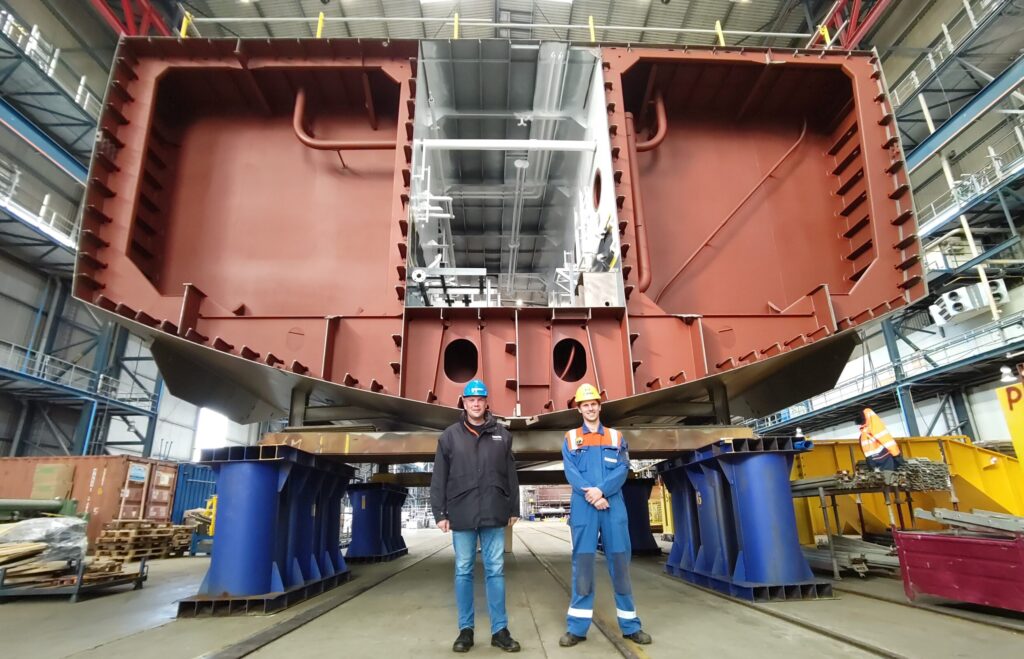
Jimmy Post (31) works as Assistant-Foreman in the piping department. “I work on the pre-outfitting phase, supervising a team of about ten pipe fitters and two pipe welders. These are two separate and quite specialist jobs; it is quite rare to have someone who can do both. We get all the information we need from Marco, and then we work week-by-week to get that done. All our work gets installed into the sections before these go to the painters.”
Jimmy’s role often brings him into contact with classification societies and clients’ representatives. “This is for the inspections of the work we have carried out. For this YN478 project, Lloyd’s Register looks at it from a ‘rules and regulations’ perspective, and the client’s representative looks at things that are specified in the contract. These inspections happen per section, and it is at that moment that you see how important it has been that all the different fabrication disciplines have worked well together.”
Contrary to Marco’s 16 years at Damen, Jimmy is still in his first year at Vlissingen-Oost. “My last job was also with piping, but in the petrochemical industry. In that job, every day was almost the same. Since starting here in March, I have been busy with a much broader scope of work; every day is different and there are so many other parameters to consider.” The YN478 project is also Jimmy’s first project at Damen: “Yes, we are having some challenges, but I am learning so much because of these challenges.” Is he pleased with his decision to swap the petrochemical industry for the shipbuilding sector? “Absolutely,” he smiles. “I have made so many steps in a very short time; it was definitely a good decision. And there are opportunities to learn more, and maybe to travel and work in different Damen yards around the world. Maybe Columbia or Germany as part of a site team; who knows?”