The cold winter months have seen Damen Naval’s F.A.S.T. (Fieldlab Autonomous Sailing Technology) project shift its operations to the less exposed environment of hall number 1 at Vlissingen-Oost. With a wide range of activities taking place, this time indoors is being well spent. The vessel’s diesel engines have been removed in anticipation of the imminent delivery of the two new electric motors. Once installed, these will provide the same amount of power as the old diesels. “We will therefore be able to sail as fast: 22 knots,” says F.A.S.T. Project Leader Jochem Nonhebel. “But, just as we see with cars, the battery package provides less range than diesel power.”
Jochem and the F.A.S.T. team have also been busy working on the vessel’s sensor equipment. This includes experimentation with LIDAR and RADAR sensors which will be used at a later stage in the project to assess automated docking operations and military operations such as launch and recovery of unmanned surface vehicles.
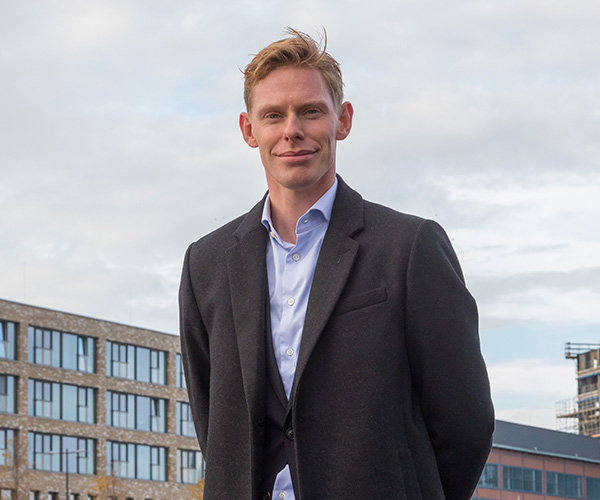
Jochem: “And we are expanding the camera setup with the addition of an infra-red camera; this should open up the possibility to carry out testing during the night and foggy conditions.” Increasing the scope of the vessel’s sensor equipment has meant that the F.A.S.T. project has had to pay greater attention to data handling, as Jochem explains: “You can imagine that many sensors require a strong and robust data infrastructure. For this reason, we are aligning with our own IT department to upgrade the project’s data infrastructure.”
For those readers wanting to take a closer look at the nine-metre long F.A.S.T. vessel (a 1990-built Damen Stan Patrol 900), this is now possible by clicking on this link which will take you to an interactive 3D scan of the vessel. Such a scan has multiple uses, Jochem adds. “We use it for engineering, PR and communication purposes. This can be for our own design work as well as a great tool to communicate with subcontractors. Furthermore, we now have quite a few of these scans so we can see how the ship has evolved.”
The 3D scan is linked to the ‘digital twin’ that has also been produced. “The digital twin is an artificial representation of how the vessel should look like when completed,” Jochem explains. “By combining the digital twin with the 3D scans, we can validate whether or not we have been building to the original design. It ensures that we maintain a high level of quality of the products that we make.”
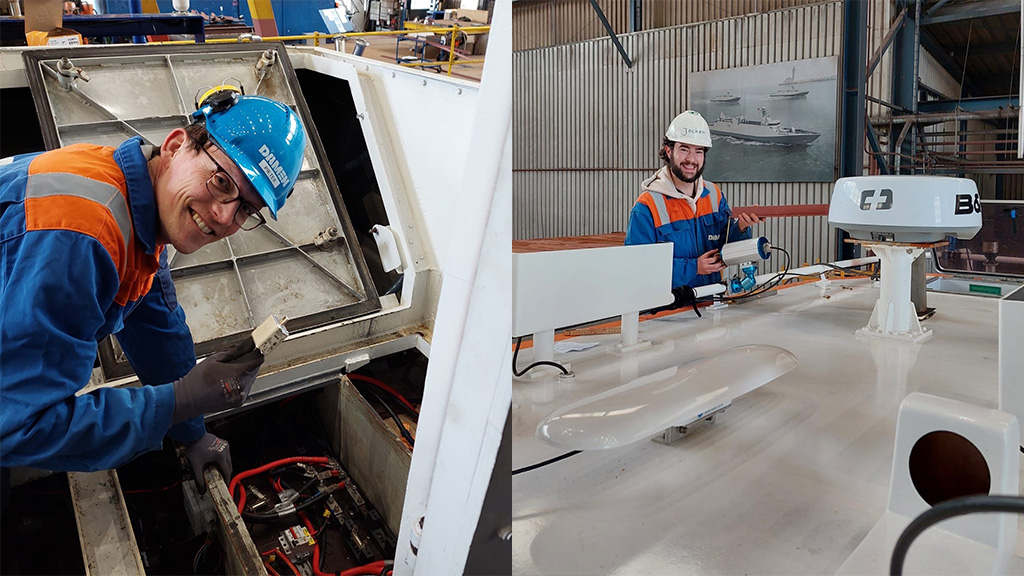
As mentioned in the previous Schelde Schakels, the F.A.S.T. project has been joined by a number of students. The project is starting to reap the rewards of their involvement. Notable mentions include Matthijs Dirksen from HZ University and Godert Notten from TU Delft. “Matthijs is working on ‘sensor fusion’, and is drawing on his data science background to turn raw data into information for autonomous operations,” Jochem says. “And Godert has started his work on a collision avoidance algorithm – this is in fact the algorithm that takes the role of helmsman. It is super important for us to have an insight into how this works because now we can much better estimate the risks that come with unmanned operations.”
With the warmer days of spring just around the corner, the F.A.S.T. team is looking forward to getting back out onto the water. “We aim to do structural work as much as possible during the winter; summer and autumn are the seasons most interesting for experiments and testing. Because then we have both hot and sunny days as well as rainy and stormy days,” notes Jochem. “This will stress the ship systems as much as possible, which is good to see their limits.”